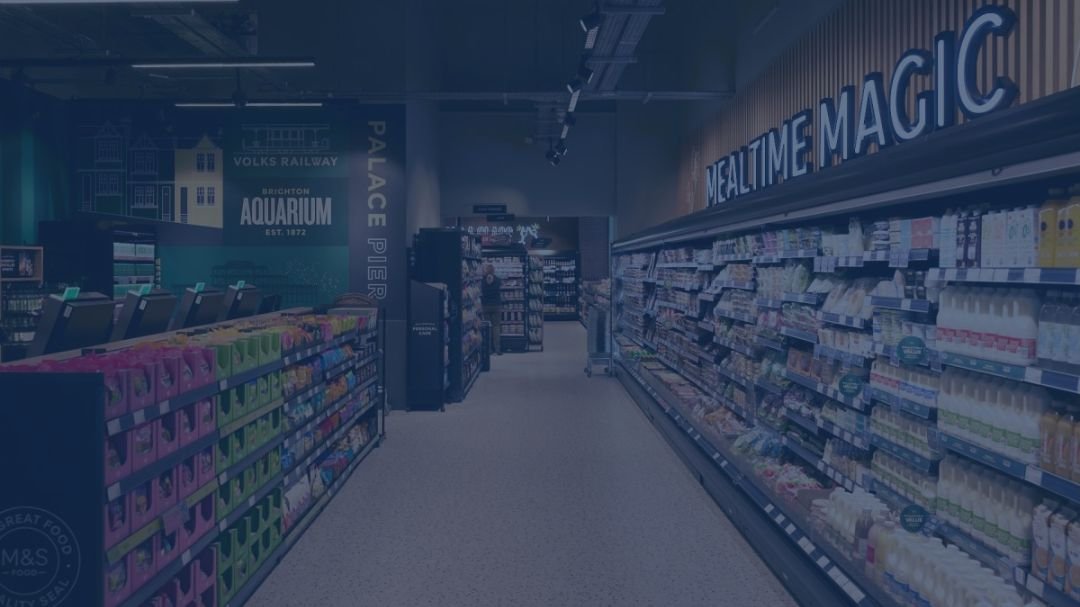
Delivering Subfloor Precision & Moisture Control in Retail Environments
M&S Clapham South
Universal Flooring Solutions (UFS) was appointed to undertake a comprehensive flooring refurbishment for the M&S store in Clapham South — a high-traffic urban location spanning 450sqm. This store had experienced long-term subfloor degradation, largely due to persistent leaks from refrigeration units. The flooring had become unstable and required a complete strip-out and reinstallation, both front and back of house.
Our team executed the project over a focused three-week schedule, combining technical expertise in subfloor preparation with the integration of premium flooring systems. We leveraged our specialist knowledge in moisture management to install a robust and resilient flooring solution that not only enhances the store’s visual appeal but also ensures long-term performance, hygiene, and safety in line with retail standards.
Working closely with Murexin and Tarkett, we delivered a flooring upgrade that addressed years of underlying moisture issues and met the operational demands of a busy commercial food retail space.
Precision-Driven Retail Flooring Renewal at M&S Clapham South
To meet the unique demands of this complete store refurbishment, UFS conducted a comprehensive assessment of the site conditions, identifying areas of subfloor failure caused by prolonged moisture exposure. We implemented a bespoke flooring solution that not only restored the store’s structural integrity but also elevated its operational durability and appearance.
From high-performance subfloor preparation to moisture mitigation and premium surface installation, this project showcases our ability to deliver tailored solutions in challenging retail environments. The following sections break down the key phases of this transformation.
-
Prior to installation, UFS conducted a comprehensive assessment of the Clapham South site to evaluate the condition of existing floor coverings and underlying substrates. Years of leakage from refrigeration systems had compromised key areas of the screed, requiring specialist intervention.
Our Solution:
Full uplift of failed floor coverings using ride-on stripping machinery to ensure efficiency and minimise manual handling.
Diamond grinding of the subfloor to remove deteriorated screed, contaminants, and ensure optimal adhesion conditions.
Application of a pre-preparation smoothing compound to flatten and stabilise the substrate ahead of moisture management measures.
This phase ensured a robust, even foundation, essential for long-term performance in both front-of-house and back-of-house zones.
-
Given the historical moisture damage, UFS implemented a targeted moisture control solution to protect the new flooring from future degradation. The selected system provides high tolerance to residual moisture levels and reinforces subfloor integrity.
Moisture Management Measures:
Installation of Murexin MS-X3 Damp Proof Membrane (DPM) to create a durable moisture barrier, tailored to high-risk zones affected by refrigeration.
Seamless integration with the substrate to prevent delamination and ensure full compliance with commercial flooring specifications.
This ensures that moisture-related movement, bubbling, or adhesive failure will not compromise the longevity of the floor system.
-
With moisture protection in place, we applied Murexin FMA fibre-reinforced smoothing compound to achieve a resilient, level surface across the entire 450m² area. This provided a stable, load-bearing platform ideal for commercial foot traffic.
Installation Benefits:
Excellent flexural and compressive strength to accommodate dynamic loading and frequent cleaning cycles.
Minimal shrinkage and crack resistance, ensuring dimensional stability under varied temperature and humidity conditions.
Installation of the final floor coverings using Murexin 499 high-strength adhesive, selected for its compatibility with commercial vinyl and its superior bond strength under high-use conditions.
-
Every component of this specification was chosen to meet the operational demands of a busy M&S store. The materials used meet or exceed safety regulations for slip resistance, hygiene, and performance under mechanical and pedestrian traffic.
UFS Compliance-Driven Approach:
Use of slip-resistant surfaces in high-risk areas to meet EN 13845 safety standards.
Compatibility with HSE guidelines and commercial flooring compliance protocols.
Seamless finish across customer-facing and operational areas to eliminate trip hazards and improve staff workflow.
-
This complete renewal project was executed with a focus on aligning visual design with the M&S brand environment, while ensuring minimal disruption to ongoing operations.
Our Execution Strategy:
Phased works and careful contractor coordination ensured completion within the scheduled three-week timeframe.
Premium material selection that blends resilience with contemporary aesthetics, ensuring consistency between customer areas and back-of-house zones.
Precision installation across all transitions and interfaces to maintain spatial flow and brand cohesion.
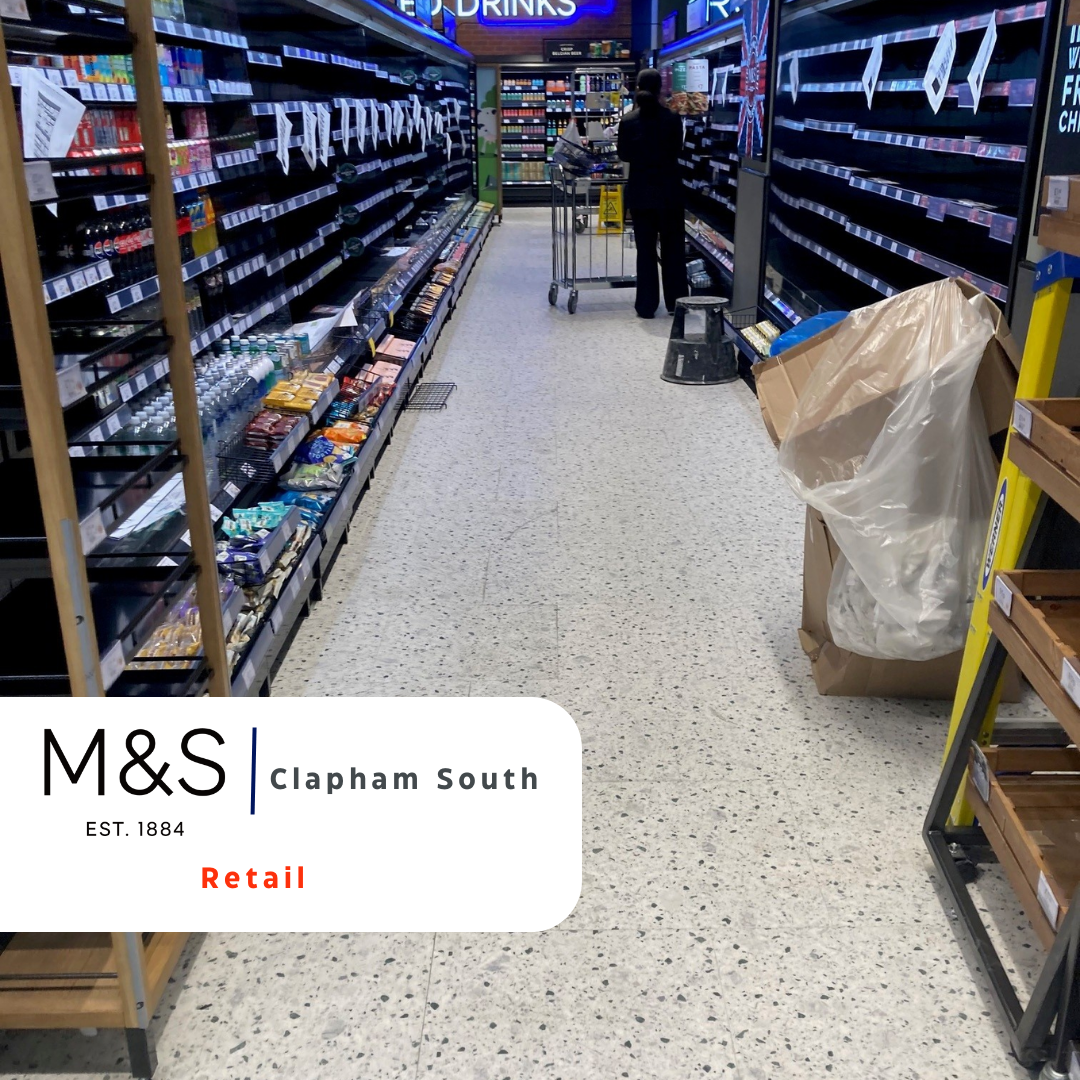

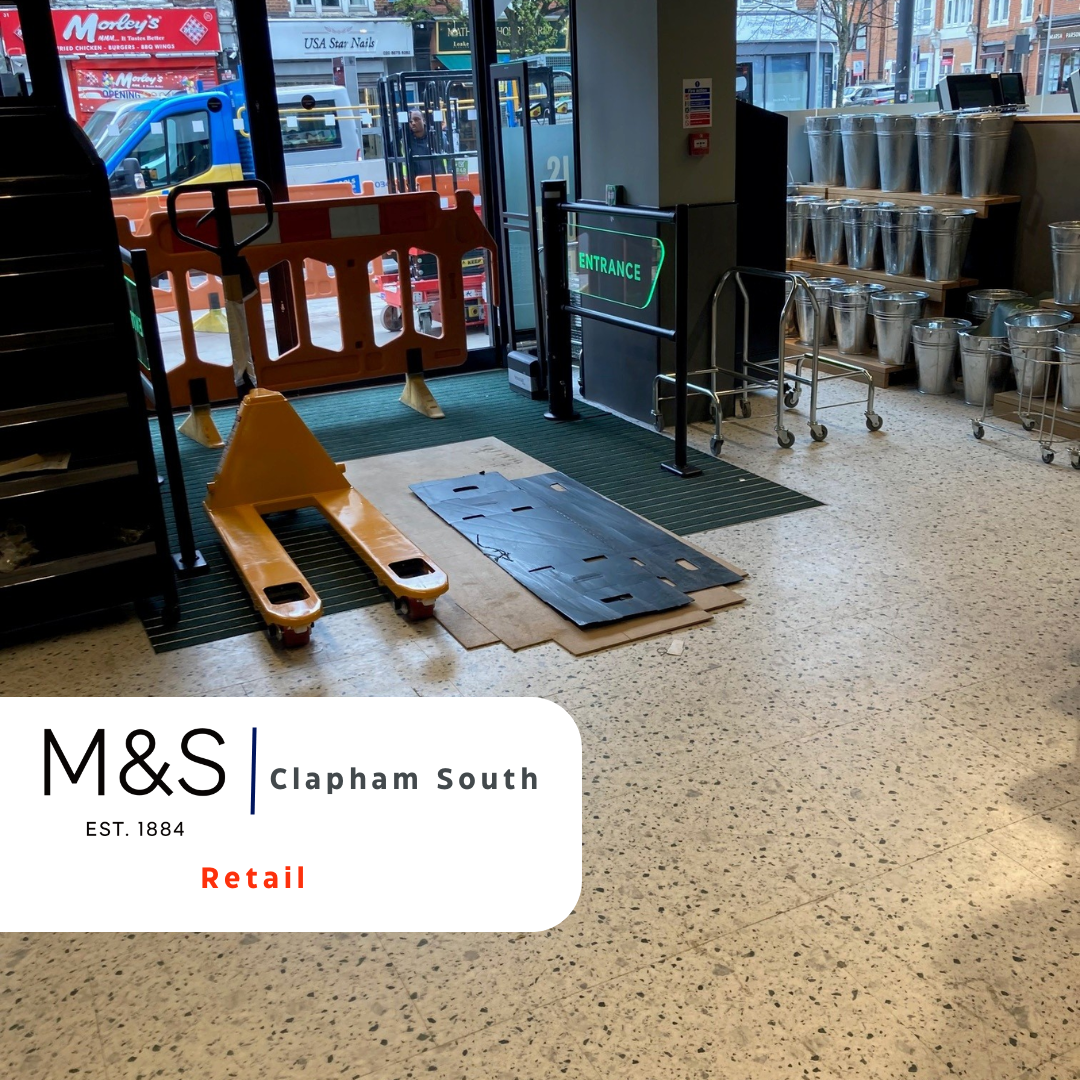

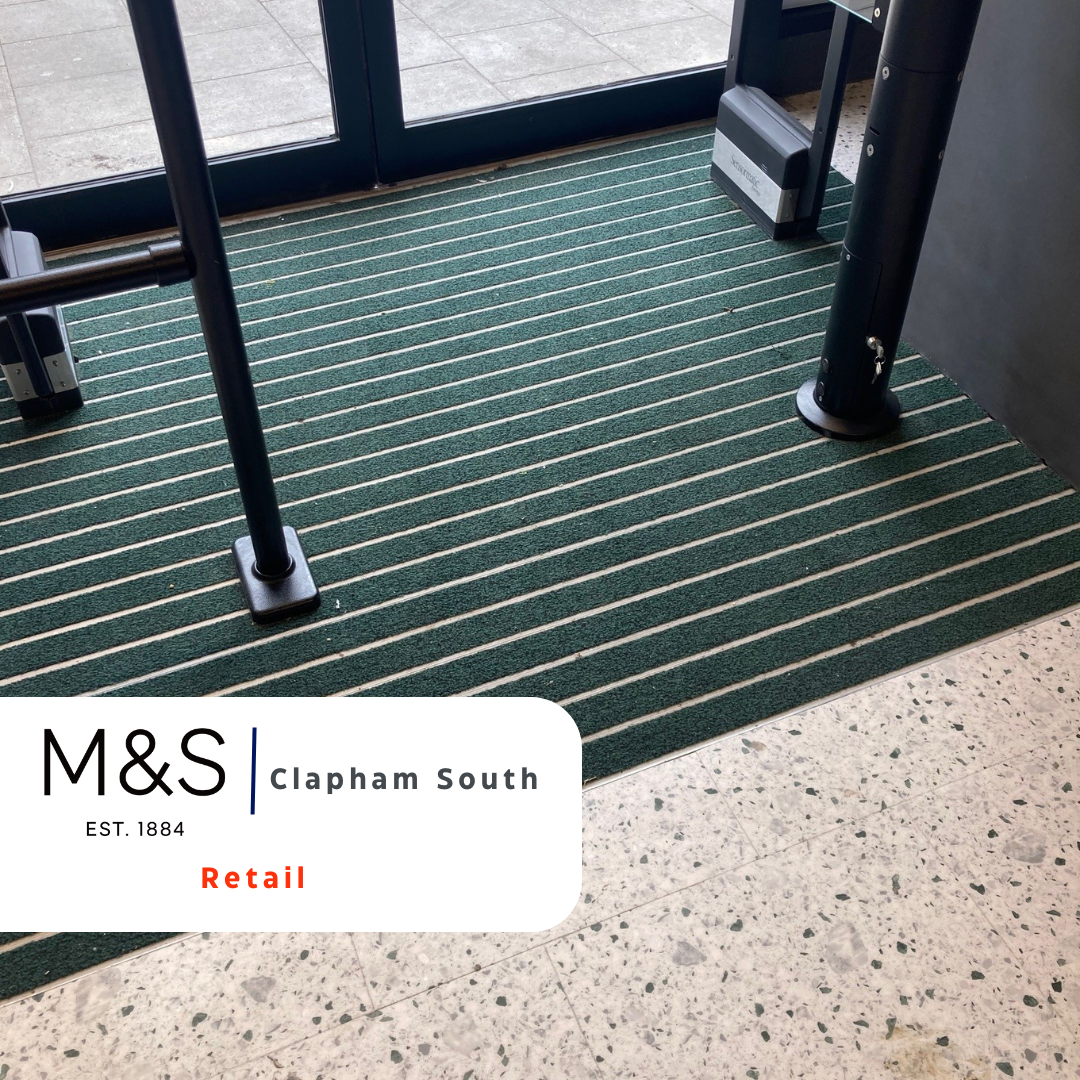
Collaboration with Expert Partners
Universal Flooring proudly collaborates with some of the most esteemed names in the flooring industry to achieve unparalleled results. For this project, we partnered with industry leaders to ensure the highest standards of quality and durability.
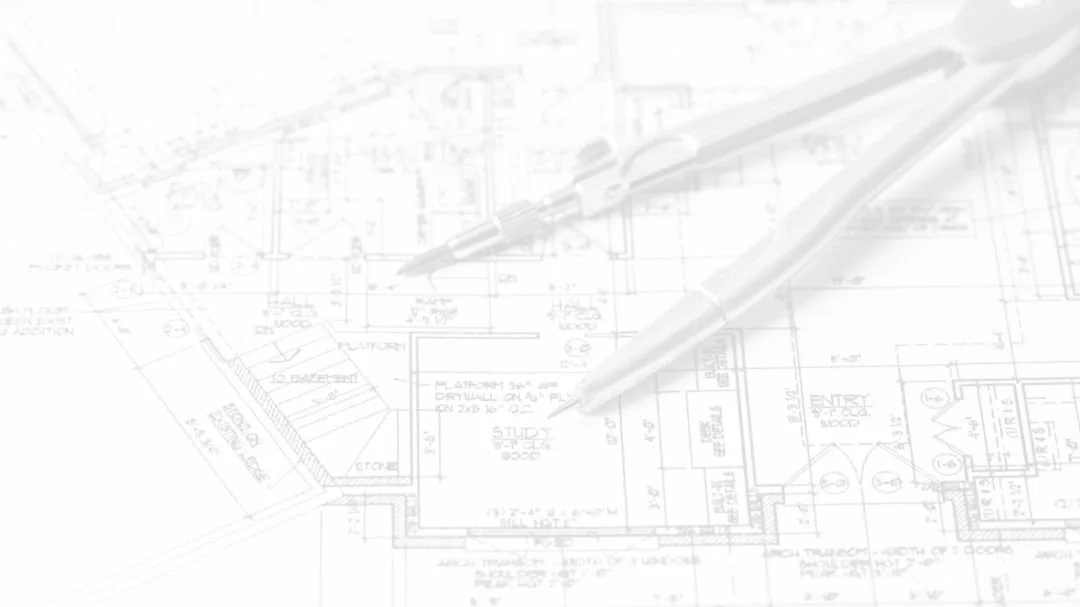
Contact us.
Transform your retail or hospitality space with our expert flooring solutions. Whether you need durable, stylish flooring for a high-traffic area or a custom design to enhance your brand's appeal, our team is here to help. Book an onsite survey with one of our trusted specialists today and discover how we can elevate your space with flooring that’s built to last!